Новые тенденции в кабельной промышленности повышающие уровень контроля качества ПВХ-пластикатов привлекают к себе все больше внимания. Но так ли все однозначно, как представляется это широкой кабельной публике? Портал RusCable.Ru продолжает подробно изучать особенности производства полимерных материалов и общаться с ее ключевыми представителями. Герой нашего нового интервью знаком уже большинству из вас.
Денис Фомин, заместитель генерального директора инновационного предприятия «ЭКО Компаунд Групп», побеседовал с Александром Гусевым, генеральным директором медиахолдинга «РусКабель», на самые острые темы, беспокоящие кабельный рынок. В большом интервью, Денис Фомин рассказал об истории своей карьеры, тесно связанной с историей развития отраслевой химической промышленности; представил новую точку зрения от рынка полимеров; подискутировал на вопросы контрафакта и причин его присутствия; подробно остановился на развитии, деятельности и планах одного из самых быстрорастущих и перспективных предприятий-компаундеров России – «ЭКО Компаунд Групп».
Компания уверенно начала свою деятельность на рынке разработок и производства инженерных пластикатов и компаундов в 2018 году. За счет развития НИОКР и плотной работы с отраслевыми Министерствами, накуоемкими предприятиями, НИИ, профессионального коллектива – «ЭКО Компаунд Групп» стремительно набирает темпы в достижении лидирующих позиций на рынке полимеров для кабельной, строительной, дорожной, автомобильной и других отраслей. Помимо уникальных и инновационных разработок, компания способна обеспечить выпуск массовой продукции. Производство компании, расположенное в г. Прохладный, имеет крупный парк современного оборудования с общей мощностью выпуска 10 тысяч тонн в год. В июне 2019 года, в г. Саранск, компанией была открыта вторая производственная площадка с мощностью выпуска 5 тысяч тонн в год, ориентированная на производство безгалогенных компаундов, сшитого полиэтилена, ТЭП для кабельной продукции.
Приглашаем вас к прочтению и обсуждению!
— Денис, рад вновь видеть Вас в качестве собеседника в новом интервью для нашего портала. Вы с командой RusCable.Ru уже долгое время, причем не как партнер, а как настоящий товарищ. Для начала, я сегодня хотел бы больше услышать о Вашем жизненном пути. Где Вы выросли, как Вы связали свою судьбу с химической промышленностью?
— Я родился и долгое время жил в городе Стерлитамак, Республике Башкортостан. Это один из центров химической промышленности России, в котором находится более 5 химических производств. Это такие компании, как «Синтез-Каучук», «Сода», «Каустик» (в 2013 г. переименован в «Башкирскую содовую компанию»), «Стерлитамакский нефтехимический завод», ФКП «Авангард».
Основным промыслом и главной причиной возникновения города, были огромные залежи соли. Наличие этих залежей послужило причиной для образования компании «Каустик». Компания производила каустическую соду, дихлорэтан, винилхлорид, поливинилхлорид. Именно туда я пришел работать после института. Я закончил стерлитамакский филиал Уфимского государственного нефтяного технического университета (УГНТУ), по специальности «Инженер автоматизации технологических процессов и производства».
Я начал работать наладчиком в цехе по выпуску оконных конструкций. Через год отправился к начальнику производства, и мне предложили должность инженера-технолога смены в цехе № 8, который занимался переработкой ПВХ в плёнку и кабельные пластикаты. С 2000 года я стал сменным инженером-технологом этого, как мне тогда казалось, громадного цеха, состоявшего из трех корпусов.
Прошел еще один год, за который я успел пройти несколько стадий в своей работе. И вдруг в цехе меняется руководящий состав: уходят начальник цеха, заместитель начальника цеха по технологии. Часто вспоминаю об этом периоде своей карьеры, ведь именно тогда мне и предложили должность заместителя начальника цеха по технологии по направлению кабельных пластикатов. Я согласился. С 2001 года начался мой путь в переработке ПВХ в кабельные пластикаты. Следующие 7 лет я отдал этому цеху.
— Вы знали своих основных потребителей тогда? Общались с представителями рынка?
— Это была одна из задач технолога − иметь коммуникации и знать, что происходит на рынке. Вообще, этот период моей работы для меня строго поделен на «до» и «после».
«До» был цех, производство кабельных пластикатов. Он выпускал 2000 тонн продукции в месяц. Ее продавали тем, кто сильно просил или обратился первым. «Старая школа» кадров не умела продавать наш продукт в новых условиях экономических отношений.
«После» «Каустик» становится Акционерным обществом. Новые управленцы ставят первостепенную задачу – продавать. Они находят «Химинвест», московскую компанию. Именно через нее был налажен основной сбыт всей продукции завода. Мы разработали несколько новых марок, запатентовали и запустили. Я являюсь одним из авторов нескольких патентов на «Каустике». И вот мы уже в круглосуточном режиме изготавливаем 2500 тонн продукции ежемесячно, после производство вовсе увеличилось до 4500 тонн продукции в месяц.
В таком бодром ритме мы успешно работали до 2007 года, пока руководство не посмотрело на результаты и не решило продавать все само, имея уже отлаженную систему, которую создала «Химинвест». Однако, специалисты «Химинвест» не растерялись и после ухода от «Каустик» основали собственное производство ПВХ-пластикатов: «Башпласт».
В 2008 году «Башпласт» был зарегистрирован как производственное предприятие, с нуля был построен завод. И так как учредители новой организации меня давно знали, они предложили мне возглавить техническую часть нового предприятия. Уже потом я занял должность генерального директора, с 2013 по 2015 успешно работал на ней.
— А почему Вы решили уйти с «Башпласт»?
— На самом деле, это больше черта моего характера. Здесь были все те же причины, что и в момент моего ухода из цеха оконных профилей на «Каустике» − рано или поздно наступает период, когда я достигаю целей проекта, когда понимаю, что сделал все что мог, когда дальнейшего развития – либо я не вижу, либо оно намеренно сдерживается. В таких случаях я выбираю идти дальше.
— То есть, Ваше видение развития разошлось с концепцией учредителей?
— Да. Когда уровень производства и сбыта на «Башпласт» вырос почти на 60%, мы вышли на определенно плато. Мне предложили остановится и осмотреться на этом уровне и проанализировать изменения рынка. Учредителям это казалось разумной осторожностью, а я считал, что она напрасна, я хотел развития.
— Сегодня Вы являетесь одним из создателей и руководителей перспективного молодого предприятия «ЭКО Компаунд Групп». Сейчас, особенно в рамках меняющихся правил нашей промышленности, очень интересно узнать о Вашем опыте. Как Вы оказались у истоков новой компании?
— Все началось еще в 2018 году. После своего ухода из «ТехИнвест-М» я обсуждал с Вами свои мысли и идеи о создании предприятия, находящегося в непосредственной близости от кабельного завода или в его прямом управлении. Тогда в ходе дискуссий и было предложено познакомится с Юрием Ежелевым и Николаем Зинченко.
Коллеги из компании «КабельСтар» были очень хорошими потенциальными инвесторами. Они посчитали мое предложение интересным и запустили будущий «ЭКО Компаунд Групп» в работу.
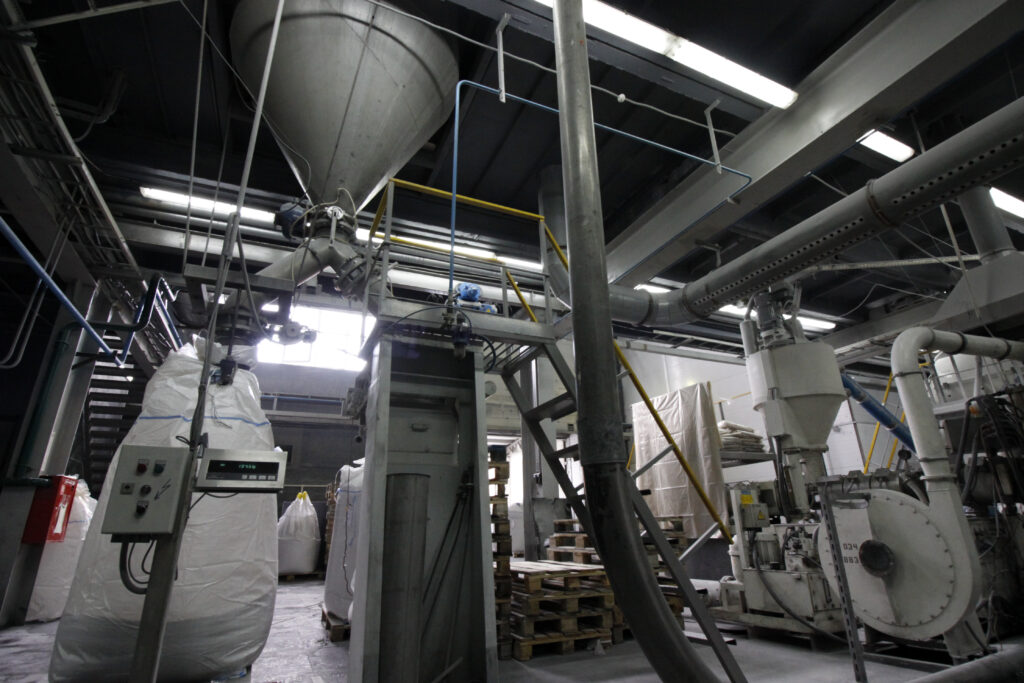
— На рынке все явственней звучат мысли о том, как это выгодно и грамотно для кабельного завода – иметь свое производство полимерных материалов.
— Это очень тонкий момент. Да, многие задумались об этом. Отчасти это выгодно, но только при наличии грамотного менеджмента и хороших технических специалистов, способных запустить оборудование, поддерживать его в соответствующем состоянии. Я уже не говорю про химических специалистов.
— Это целая наука, без знающих и опытных сотрудников здесь многое не сделаешь.
— Конечно. Успех такого предприятия будет заключаться в его способности производить полимерные материалы по соответствующим рецептурам на каждую отдельную конструкцию кабельного изделия. Очень трудно выходить на большой рынок и пытаться перебить по цене крупных игроков, которые имеют огромную производительность, сырье по скидкам, дешевую рабочую силу и другие преимущества. Недостаток таких производителей кроется в специальных марках, спрос на которые небольшой: гиганты не могут позволить себе производить их, потому как ориентированы на универсальные. В связке «кабельный завод – производство материалов» получается настоящий симбиоз, где оба предприятия работают на одну цель. Такой кабельный завод может не боятся пробовать себя в новых узкоспециализированных нишах.
— В названии вашей компании слово «Групп» фигурирует не просто так? Вы имеете несколько производственных площадок?
— Да, в данный момент две. В Прохладном у нас сильная лаборатория по ПВХ-пластикатам, а в Саранске − по полиолефиновой группе, каучуку.
— Возможно, совсем скоро нашему порталу представится возможность своими глазами увидеть вашу производственную площадку в Прохладном. С интересом буду ждать этого.
Предлагаю продолжить нашу беседу в другом направлении. Совсем недавно в рамках расширенного заседания Ассоциации «Электрокабель» активно обсуждалась тема контрафакта в полимерных материалах для кабельной промышленности, выдвигались предложения по ужесточению контроля поставщиков полимерной продукции, организации целой системы по добровольной сертификации. Вопрос: есть ли, на Ваш взгляд, в этом такая сильная необходимость?
— Скажу честно, как технический специалист, управляющий предприятием по производству полимерных компаундов, и как человек, близкий к кабельной промышленности, я не понимаю ажиотажа вокруг необходимости создания нового стандарта. Зачем стандартизировать то, что и так есть, что заложено в технической документации предприятия изготовителя? Все компаундеры выпускают пластикаты в соответствии с техническими условиями, хорошими и грамотными ТУ, по которым выпускается продукция, способная выдержать необходимые условия, предусмотренные ее назначением.
Запрос на «контрафакт» идет с кабельного рынка. Не редко моим коллегам приходится слышать такое: «Пусть это будет что угодно, пусть от ППО только название останется, лишь бы экструдировалось нормально, на остальное плевать. Мы и без маркировки свой кабель продадим. Нам нужен материал, проходящий по цене. А вот под сертификацию уже нормальный понадобится, это да».
Вопрос не в отсутствии стандарта.
— Обилие контрафакта порождает сам потребитель?
— Я всегда это говорил. Спрос диктует предложение. Вот, например, недавно вышла статья Виктора Геннадьевича Николаева «О борьбе с контрафактом кабельных композиций и кабельных изделий». В ней многое сказано про стандартизацию и старый ГОСТ. Да, стандарт старый, но на что это влияет? Заложенные в нем методики действуют до сих пор, они перенесены во все настоящие ТУ на современные компаунды, с добавлением отдельных характеристик вроде трудногорючести, низкодымности и так далее.
Почему же тогда никто не говорит про ТУ на пластикат НГП от 1986 года? А вот ГОСТ 1972 года, который у всех на устах, якобы, полностью устарел. Да, марки пластикатов, заложенные в него, уже несовременны, но методики, показатели до сих пор повсеместно используются. Потом вышла серия материалов НГП пониженной горючести. В них был введен кислородный индекс как определение трудногорючести полимеров. НГП до сих пор выпускается по старым рецептурам. Другое дело, что сам рынок НГП небольшой, на нем нет особой конкуренции. А ППО – большой рынок, у него высокий уровень потребления. Там идет очень большая конкуренция по цене.
— То есть позиция компаундеров такая: мы производим ровно то, что вы от нас требуете?
— Именно так. Есть пример очень грамотного кабельного производителя, который в свое время меня очень впечатлил. «Электрокабель» Кольчугинский завод» уже около 5 лет покупает материал по собственным техническим требованиям. Им не нужен стандарт, так как они на каждую марку полимерных материалов сформировали собственные требования. Они говорят потенциальным поставщикам прямо, что необходим конкретный материал, к которому есть перечисленные требования. Не подписываетесь под требованиями – не работаем. Подписываетесь – поставляете и выдерживаете постоянный контроль. Если не выдерживаете – получаете возвраты и штрафы.
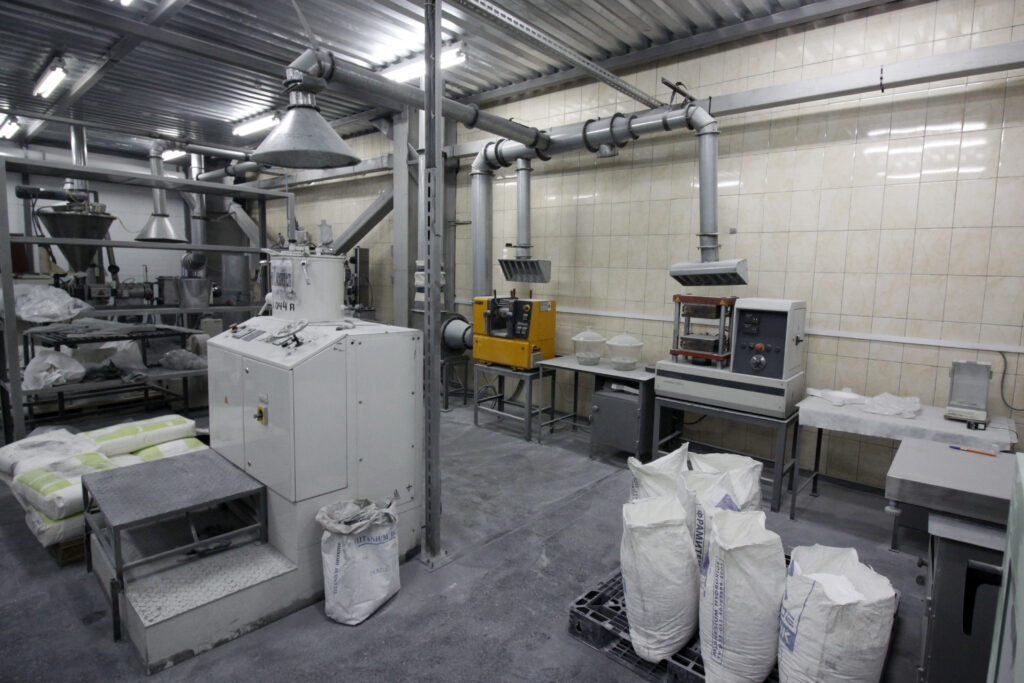
— А как быть с другой стороной монеты? Когда даже авторитетные заводы закупают полимеры у компаундера, по его ТУ, а потом на испытаниях конечной продукции получают показатели, отличающиеся от заявленных. Потребитель это испытывает, возвращает всю продукцию, накладывает огромные штрафы. То есть кабельный производитель должен как-то себя защитить. Как ему это сделать?
— Подписывать дополнительное соглашение, обязывающее поставщика материалов предоставлять именно ту продукцию, которую он заявляет.
— Это подразумевается законом. Если продукция поставляется по конкретному ТУ, то все поставки соответствуют. Однако в реальности это не всегда так.
— Я объясню, почему. Первое и самое главное: это недоработка технической службы кабельного завода с поставщиком. Крупные производители компаундов создают универсальные материалы, которые полностью подойдут в 80% случаев, но не для всех вариаций кабельной продукции. Кабельный завод покупает этот универсальный продукт, думая, что он подойдет во всех необходимых ему случаях, но не убеждается в этом предварительно. Те самые 20% вариантов, когда материал применяют в тех изделиях, для которых он не предназначен, и формируют все эти проблемы, о которых так шумит рынок. Здесь необходима совместная плотная работа технолога кабельного завода и технолога химического производства, чтобы все тонкости учитывались.
На любом кабельном заводе существует процедура постановки материала на производство. Любой новый материал проходит несколько стадий: входной контроль материала, технологическое опробование, испытания полученного изделия на соответствие требованиям КПП. Что мешает эти процедуры выполнять и предъявлять заводам-компаундерам соответствующие претензии?
— Крупные заводы так и делают. Но возмущаются – почему они должны тратить на это свои финансы, ресурсы и время.
— Есть определенный процент производителей компаундов, которые под видом хорошего продукта продают удешевленный материал. Понятно, что большинство заводов не могут себе позволить проводить проверку каждый месяц, чтобы защититься от таких производителей. Но ведь можно заключить договор с поставщиком, при котором его продукция будет ежеквартально проверятся в лаборатории на аутсорсе, а при наличии отклонений – издержки будут возмещаться компаундером.
— Чем вызвана легкомысленность со стороны некоторых заводов к качеству того, что они покупают? Это отсутствие понимания, знания или просто экономическая политика?
— У кого-то не хватает специалистов, чтобы проводить эту работу, ведь для этого на производстве должен быть соответствующий сотрудник. Еще у кого-то может быть такое видение бизнеса: «покупаю дешево, продаю и зарабатываю, а дальше будь что будет». Есть те, кто думает, что покупает хороший материал, а им поставляют некачественный.
— А существует ли в полимерной промышленности такое понятие как интеллектуальная собственность? Есть ли у вас такая проблема как подделка?
— Это сейчас называется красивым словом «прототипирование». «Подделка» у химиков – это не совсем то, что понимается под этим словом. Берется материал, исследуется и раскладывается на составляющие компоненты. Хороший специалист, понимающий конечные характеристики изделия, его полимерную основу, создает такой же материал по собственной рецептуре, исходя из знаний полимерной переработки. Даже если провести термогравиметрический анализ и дифференциально сканирующую калориметрию, увидеть пики, максимально точно понять, что содержит в себе полимер – все равно очень тонкие моменты будут индивидуальны. Если очень захотеть, все равно не выйдет обвинить кого-то в подделке.
Возвращаясь немного к теме входного контроля полимерной продукции на кабельном заводе, отмечу, что есть смысл идентифицировать материалы с помощью «отпечатка». Для того, чтобы проверять поставщика на то, что он направил именно ту продукцию, о которой он договорился с заводом. Во время первой поставки нужно сделать слепок, сжечь его в термогравиметрическом анализаторе и посмотреть пики, гистограмму выделяющихся веществ. Повторяя эту процедуру на следующих партиях, легче определить изменение соотношений или компонентов. Такая процедура будет занимать 15 минут. Но есть одно «но» − очень дорогое оборудование.
— Об этом уже не раз говорилось на деловых мероприятиях, однако, погоня за экономией у большинства производителей, не стыкуется с предлагаемой Вами практикой.
Давайте поговорим немного о ценообразовании. Чем Вы можете объяснить то, что цифровые марки ПВХ-пластикатов приблизились по своей цене к западным безгалогенным компаундам?
— Себестоимость хорошей продукции сама по себе всегда высока. Цифровые марки должны соответствовать требованиям для широкого спектра изделий как универсальный материал, идеально работающий в 95% случаев. Дополнительно это обуславливается такими моментами: чтобы материал смог выдержать испытания на старение, нужно применять более дорогой диизононилфталат (ДИНФ), линейный пластификатор. Потому что диоктилфталат (ДОФ) не способен обеспечить должных качеств. Чтобы получить низкий уровень дыма и хороший кислородный индекс, нужно добавлять гидроксид алюминия, что повышает цену продукта в два раза.
— А как обстоят дела с импортом химических компонентов?
— ПВХ-пластикаты производятся 100% из российских компонентов. Безгалогенные компаунды имеют порядка 60% импортных компонентов, потому что модифицированный полиэтилен в России не производится, этиленвинилацетат, полиолефиновые антиоксиданты тоже.
— В этом году «СИБУР» открыл свое производство диоктилтерефталата (ДОТФ). Вы используете его в производстве?
— Мы заказали у них партию на пробу, провели лабораторные исследования, протестировали опытные партии. Его можно применять, но на определенные рецептуры. Есть свои плюсы. Например, ДОТФ − это такой же низколетучий пластификатор, как ДИНФ. С его применением получается хорошее сохранение свойств. Но есть и минусы: ДОТФ плохо совместим с хлоропарафинами, которые критичны в рецептуре НГП, также его пластифицирующая способность ниже, чем у ДОФ, соответственно ДОТФ нужно добавлять больше. От этого страдают рецептуры.
Мы его взяли только потому что необходимо подготовится к новым реалиям. Есть опасность, что скоро ДОФ станет очень мало на рынке. К примеру, пермский завод «Камтэкс-Химпром» в октябре этого года ДОФ на рынок не давал. Потому что в той же Перми расположилось новое производство ДОТФ компании «СИБУР».
Как это связано? В производстве ДОФ и ДОТФ необходим компонент 2-этилгексанол. В России существует всего два производителя этого синтеза: «Газпром нефтехим Салават» и «СИБУР». «Газпром нефтехим Салават» пускает 2-этилгексанол на собственное производство ДОФ. А «СИБУР» использует его в производстве ДОТФ. Обе компании перестали продавать 2-этилгексанол на внутренний рынок и «Камтэкс-Химпром» остался без сырья. Теперь они закупают его через биржу, с мирового рынка по экспортной цене, которая гораздо выше. Поэтому они не могут конкурировать по цене с тем же «Газпром нефтехим Салават». Два монополиста вытесняют конкурентов на рынке ДОФ и ДОТФ. «СИБУР» запустил свое производство в апреле, пять месяцев «Камтэкс-Химпром» продержался – еще в августе мы брали у них ДОФ. А вот в сентябре уже не стали, нас не устроила цена. Плюс, цена на ДОФ и так будет расти, учитывая положение дел и агрессивную политику выхода на рынок у определенных компаний.
— Мы затронули тему импорта компонентов для химической промышленности. А какая ситуация с экспортом полимерной продукции в другие страны?
— Пока ее нельзя назвать хорошей. Чтобы наши материалы применялись в Европе, Америке, они должны пройти сертификацию по их системе, а это очень дорого, в то время как перспективность выхода на эти рынки предсказать трудно.
— Как все мы знаем – кадры решают все. Где вы находите своих специалистов?
— Ситуация с набором персонала довольно трудная, она обусловлена как расположением наших производственных площадок, так и общим уровнем подготовки специалистов в стране. Наш коллектив пока небольшой, но это позволяет обеспечить его постоянное обучение. Конечно, мы открыты для сотрудничества, но для тех, кто готов действительно работать, развиваться, привносить новое. Таких специалистов по стране, на мой взгляд, в пределах дюжины. И все они на виду, все уже заняты.
— В чем заключается главный секрет химиков? Добавки в рецептуры, смеси, соотношения, особенные шнеки?
— Отчасти все, что Вы перечислили. Конечно, все основные рецептуры известны. Секрет кроется в синергии всех компонентов. Здесь важны их малейшие изменения, соотношения. Например, одни и те же компоненты в сумме могут давать разные эффекты при разном порядке их добавления.
— В ходе последнего «Кабельного конгресса», который проводился в рамках Cabex-2019, часто обсуждался вопрос экологии и ее защиты. В названии вашей компании первым стоит слово «ЭКО». Есть ли здесь прямая связь?
— Многие будут удивлены, но основной смысл в формулировке «ЭКО» в названии нашей компании – это стремление к экологичности в сотрудничестве с нашими партнерами. Мы не токсичны для наших клиентов. Мы не обманываем потребителя и используем в производстве нашей продукции только те компоненты, в которых уверены на 100%. Мы не играем с качеством, не идем на поводу у экономии. Наша задача – производить надежный продукт, соответствующий своим характеристикам, в которых наш покупатель может быть полностью уверен.
— Со старта работы первой площадки в Прохладном прошло уже больше года. Что за это время было вами сделано?
— Первым делом мы запустили линию по производству ПВХ-пластикатов в Прохладном. Она существовала еще до нас, но была законсервирована и не эксплуатировалась несколько лет. Наша команда провела техническое дооснащение линии, подготовила ее к запуску. Мы обучили персонал работе с этой линией и запустили в производство новые марки пластикатов, ранее не изготовляемых на ней. На «Кавказкабель» был полностью обновлен номенклатурный ряд потребляемых пластикатов, и наша площадка целиком их освоила. Кроме того, до консервации мощность этой линии составляла 250 тонн в месяц. Мы разогнали оборудование: сейчас линия работает на 100% мощности, производя 800 тонн в месяц.
Далее мы спроектировали и закупили линию для производства полиолефиновых компаундов на площадку в Саранске. Она была специально спроектирована, она имеет определенные узлы, что позволяет производить на ней широкий перечень полимерных компаундов: безгалогенные композиции, сшитый полиэтилен, резиновые смеси, этиленпропиленовые резины, термоэластопласты.
Также, мы активно развиваем наши лабораторные мощности: исследования, разработки, опытные работы. Производство полимерных материалов – это постоянные исследования. Появляются новые марки, добавки, сырье. Все их нужно опробовать, тестировать, искать альтернативы.
— Сейчас очень модной темой становится автоматизация производства и цифровизация процессов, ERP-системы. Что из этого вы внедряете или уже применяете?
— В силу того, что центр принятия решения по задачам холдинга находится по всей стране, мы находимся на гребне волны тренда ERP-систем. Мы применяем написанную для нас систему, которая позволяет дистанционно решать многочисленные вопросы и задачи в крайне удобном, оперативном и эффективном виде.
— В скором времени ваш рост приведет к тому что, вы полноценно начнете осваивать рынок. Но кабельные производства очень неохотно меняют поставщика полимеров ввиду того, что их производственные процессы уже отлажены, а работа на новом материале потребует индивидуальной настройки. Какую поддержку вы предлагаете в этом направлении?
— Мы уже оказываем постоянную техническую поддержку, для нас важен не только факт продажи. Недаром на всех наших контактных данных и в нашей рекламе всегда указывается два номера телефона. Первый – это отдел продаж, второй – технический сервис. Мы оперативно откликаемся на любые вопросы и реагируем готовым решением. В то же время для нас важно решать индивидуальные запросы предприятий. Материал есть, он соответствует, но чего вы захотите достичь с его помощью, что вы хотели бы изменить, добавить? Все это мы готовы прорабатывать, улучшать, и не всегда путем удорожания.
— Какой Вы видите компанию через три года?
— Через три года в нашей группе будет порядка пяти цехов по производству полимерных материалов. Южный регион и Поволжье у нас уже есть. Мы пойдем в Северо-Западный округ, за Урал. Основная задача – близость к конечному потребителю. К примеру, за Уралом нет ни одного производителя полимеров для кабельных заводов, которых там очень много.
— Заключающий вопрос. Вы прошли большой и сложный путь, полный бесценного опыта, достижений и интересных историй. Сегодня Вы развиваете компанию, у истоков которой стояли. Вы вдохновитель и руководитель полимерного направления, создающий свою команду, политику. Какие возможности открылись перед Вами сегодня, доступа к которым у Вас раньше не было?
— Я в этой промышленности 20 лет. Я побывал на разных предприятиях с разными структурами и задачами, и я безмерно благодарен всем им за тот бесценный опыт, который получил. Жизнь всегда вела меня только вперед, уводя от преград, которые передо мной возникали. На «Каустике» (1999 – 2007 гг.) была большая проблема внедрения новинок. Огромная бюрократическая машина стояла перед теми, кто желал развить компанию. На «Башпласт» (2008 – 2015 гг.) было совсем по-другому: мы очень четко и быстро реагировали на запросы клиентов, разрабатывали уникальные решения, но в определенный момент началось сдерживание развития направлений. «ТехИнвест-М» (2017 – 2018 гг.) ставил совершенно другую задачу – увеличение операционной деятельности, но у его коллектива не было желания меняться. В штыки воспринимались любые изменения.
Сейчас все эти проблемы в прошлом. Все идеи, которые я предлагаю, как минимум проверяются и тестируются. Только после получения ряда негативных результатов принимается решение о приостановлении движения по этому направлению. Мы развиваем совершенно новые, уникальные области работы. Например, мы изучаем вопрос девулканизации резины, сшитого полиэтилена. Есть большое количество такого материала, попадающего на выброс, переработать который невозможно, но если его девулканизировать, разрушить связи, то получится обычный полиэтилен, который можно использовать повторно. Такого оборудования и технологии еще не существует, поэтому мы проводим тщательные исследования. В целом, 30% времени на всех площадках «ЭКО Компаунд Групп» посвящено научно-исследовательским и опытно-конструкторским работам.
Когда-то Вы взяли мое выражение в оглавление нашего с Вами интервью: «Свободой надо уметь пользоваться». Сегодня мы с коллегами свободны в профессиональном плане, наш потенциал уважают и поддерживают. Настало то самое время, когда мы используем нашу свободу для того, чтобы сделать новый рывок вперед.